Category
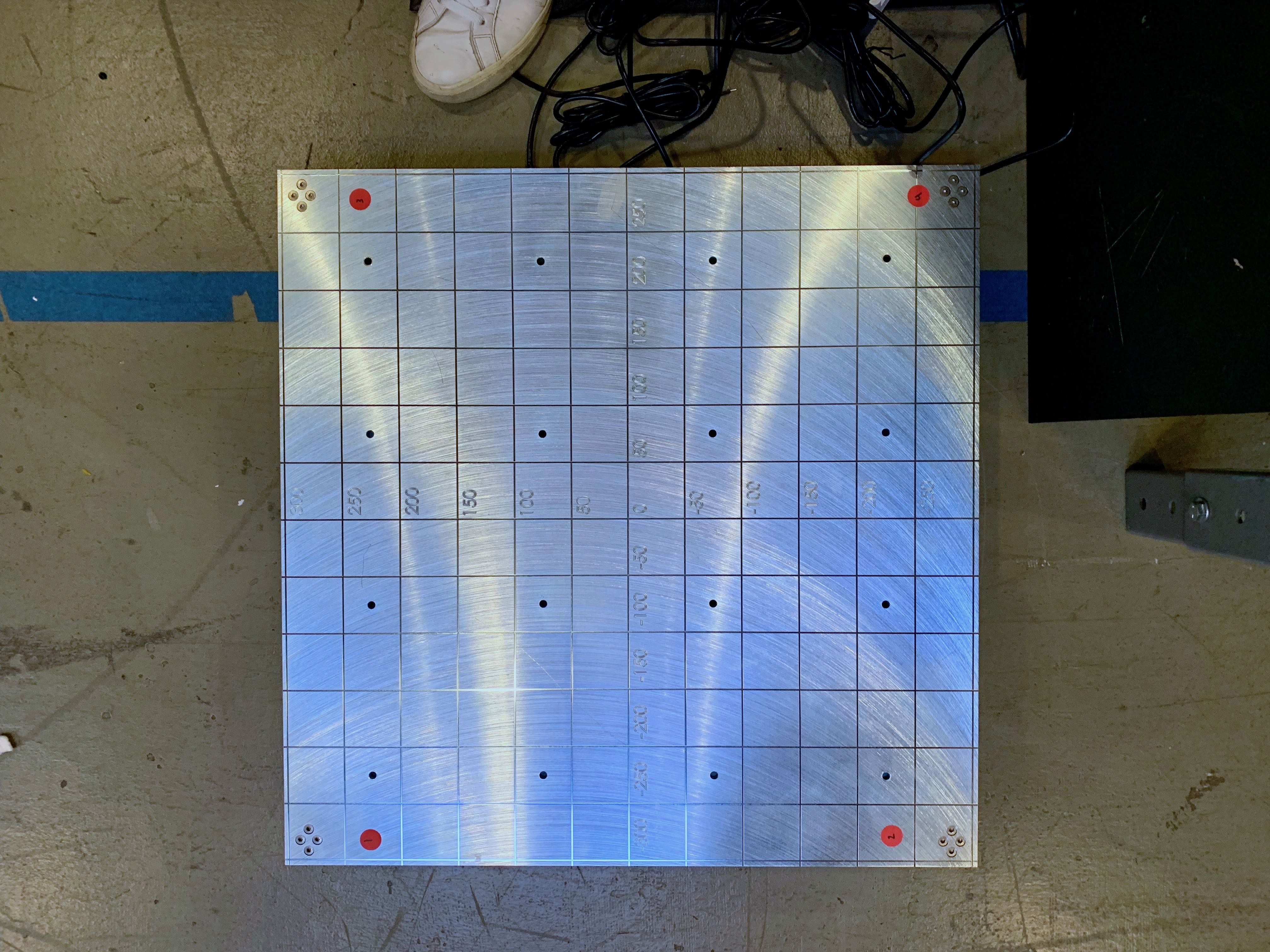
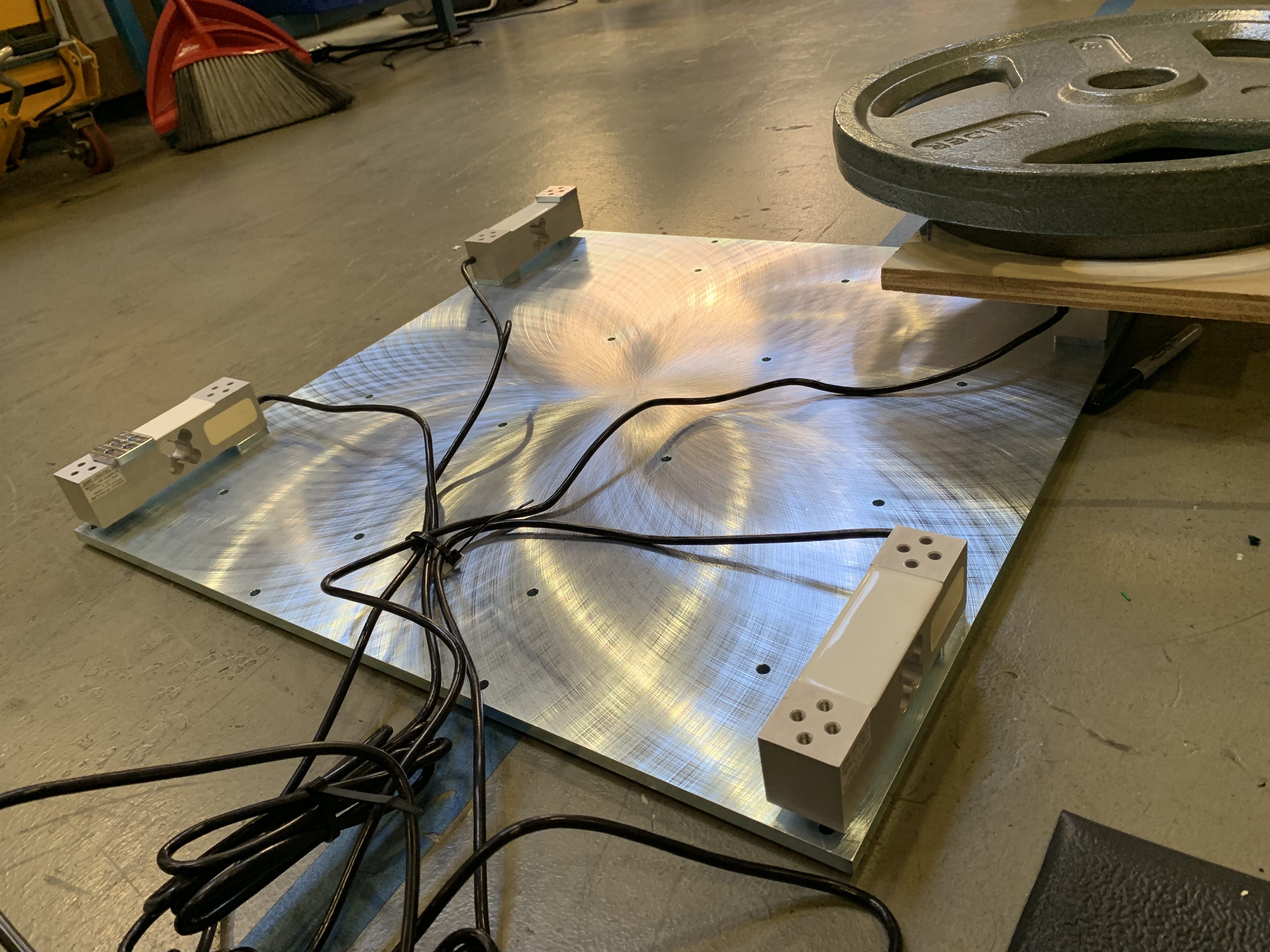
Opportunity Space
Robot CG is important for these reasons:
- Product is a very tall and heavy robot
- If the robot falls (or is pushed) it can damage itself and/or harm customer
- If CG is improperly balanced, driven wheels can slip and cause odometry/navigation errors
- CAD is a good CG approximation, but not always accurate
- Previous method for calculating actual CG were inaccurate and laborsome
- Using 4 scales to measure normal force on the wheels and manually calculating
- Scales tended to be +/-0.3kg
Design Requirements
- Scale should support:
- One robot drivetrain worth of space (preferably more)
- Loads up to at least 250kg
2. Scale should accurately report:
- Total Mass in kg
- Center of Mass in X/Y coordinates in metric units (cm, mm)
3. Scale should be able to be “tared” or zero
4. Output should be readable and understandable by humans Loads should be able to be easily loaded on and off of the scale
Design Theory
a brief overview….
CAD Design
Fabrication
Calibration
Final Product
Reflection
- Gained additional experience with Arduino and working with sensors and their outputs.
- Applied GD&T to ensure pattern features on parts would assemble.
- Learned to use design requirements to drive research and prototyping.